SAFETY EQUIPMENT TO BE USED IN A DEMOLITION PROJECT
Prior to the start of a demolition project
The engineer must complete a written survey to determine if there are any hazardous substances in the structure and asses the condition of the floors, walls, and framing to prevent a premature collapse. The completed survey must be kept on the job-site and made available upon request.
The demolition contractor is responsible for planning the wreckage of the structure, the equipment to do the work, informing worker of hazards and safety requirements, and public safety. Planning should include necessary safety equipment such as:
- Specific respirators for the job.
- Hearing protection.
- Safety nets, lifelines, and fall protection.
- Warning signs.
- Eye and face protection.
- Sidewalk sheds or canopies at all entrances.
- Water to keep material or debris wet to prevent dust from rising.
Emergency preparation
Workers should also know how to respond to possible emergencies. Emergency procedures should be devised, explained, and posted. Make sure to name all the local medical or emergency responding facilities and post it in a readily accessible location with phone numbers and addresses. Post all first aid and CPR equipment with the names of on-site certified individuals.
The demolition area should be clearly marked as such to ensure that only authorized personnel are within restricted areas of the site. All site workers or authorized personnel should be dressed in appropriate personal protective wear and be informed of safety practices and emergency procedures.`
OSHA Standards
OSHA Compliance Safety and Health Officers often face a somber task as they identify and document the violation of safety and health standards which lead up to the latest worker tragedy. Demolition worker impaled on rebar. Worker electrocuted during demolition work. Two demolition workers die of burns after flash fire at warehouse. Employee in aerial lift killed when roof collapses. However, the hazards of demolition work can be controlled and eliminated with the proper planning, the right personal protective equipment, necessary training, and compliance with OSHA standards. This Safety & Health Topics page is dedicated to the demolition workers who died on the job.
Demolition is the dismantling, razing, destroying or wrecking of any building or structure or any part thereof. Demolition work involves many of the hazards associated with construction. However, demolition involves additional hazards due to unknown factors which makes demolition work particularly dangerous. These may include:
- Changes from the structure’s design introduced during construction;
- Approved or unapproved modifications that altered the original design;
- Materials hidden within structural members, such as lead, asbestos, silica, and other chemicals or heavy metals requiring special material handling;
- Unknown strengths or weaknesses of construction materials, such as post-tensioned concrete;
- Hazards created by the demolition methods used.
To combat these, everyone at a demolition worksite must be fully aware of the hazards they may encounter and the safety precautions they must take to protect themselves and their employees.
Demolition hazards are addressed in specific standards for the construction industry.
Hazards
PLAN ahead to get the job done safely
Proper planning is essential to ensure a demolition operation is conducted with no accidents or injuries. This includes, but is not limited to:
- An engineering survey completed by a competent person before any demolition work takes place. This should include the condition of the structure and the possibility of an unplanned collapse.
- Locating, securing, and/or relocating any nearby utilities. For help, call 811 before you dig.
- Fire prevention and evacuation plan.
- First Aid and Emergency Medical Services.
- An assessment of health hazards completed before any demolition work takes place.
PROVIDE the right protection and equipment
The employer must determine what Personal Protective Equipment (PPE) will be required. In demolition operations, PPE may include:
- Eye, face, head, hand, foot protection
- Respiratory protection
- Hearing protection
- Personal Fall Arrest Systems (PFAS)
- Other protective clothing (for example, cutting or welding operations)
It is not enough to provide PPE. Employees must be trained on the selection, use, fitting, inspection, maintenance, and storage of PPE.
TRAIN all employees about hazards and how to use the equipment safely
Under the Occupational Safety and Health Act (OSH Act), Public Law 91-596, employers have a responsibility to provide a safe workplace for employees. Employers must instruct employees how to recognize and avoid or remove hazards that may cause an injury or illness based on their assigned duties. Certain OSHA construction standards require that employees receive training in specific topics. Employers must provide this safety training in a language and vocabulary their workers can understand.
Be sure your next project complies with all the applicable regulations.
We are ECG, we are safety first.
This field definitely needs some expert hands and skill. So, have you decided on what type of project you need? Make sure you research on this for a while before coming up with a decision.
We pride ourselves in providing Demolition, Abatement and Environmental Services you can depend on. (Concrete cutting, coring, green demolition, disinfection and sterilization cleaning services, asbestos abatement and more)
Contact us to get started on your next project, Call us: 562-438-7999.
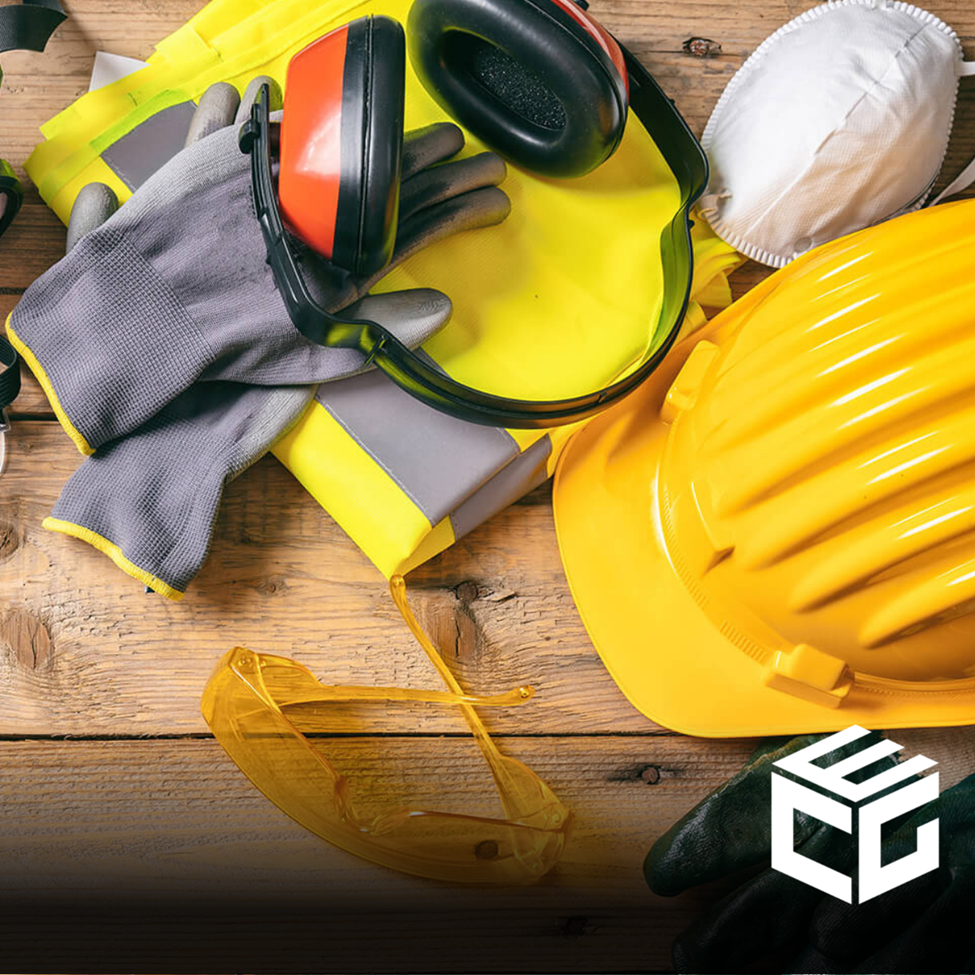